I vividly recall a job when the epoxy resin not curing issue brought everything to a halt. The flooring wouldn’t harden even after 48 hours. The resin stayed soft, sticky, and useless. The workers were upset, the client was worried, and every hour that went by meant more money and time lost. If you’ve ever dealt with epoxy, you know that curing difficulties are among the most stressful challenges in our field.
1. Why It Matters and a Real-Life Example
Epoxy resins are what make up the paints, adhesives, and flooring systems. When they don’t cure, all of the work stops. Many people are reluctant to acknowledge that the problem occurs more frequently than they realize. I had to deal with this once on a big contract to install flooring in a warehouse. The people who applied the product had mixed it according to the datasheet. The resin surface, on the other hand, remained sticky, and people couldn’t walk on it even after two days.
Curing failures are just one side of the challenge. In fact, studies show that many floors face other risks-learn more in my blog on Why 50% of Epoxy Floors Fail Within 2 Years
The effect of epoxy resin not curing was quite bad. The client had to put things in storage. The flooring crew had to stop working, which resulted in a loss of time and damage to their reputation. Every delay meant money lost for the project owner. As the R&D manager, the situation put both faith in the product and brand image at risk. There was no way of rapidly solving it.
2. Possible Solutions for Epoxy Resin Not Curing
I made a list of plausible reasons why epoxy might not cure:
- The incorrect ratio of resin to hardener could be a contributing factor.
- Inadequate mixing results in pockets of unreacted material.
- The temperature or humidity wasn’t right when it was applied.
- The raw materials used were either old or contained moisture.
- Surface contamination halts the curing process.
Industry standards also highlight the same critical factors, especially humidity and mix ratios, as noted in ASTM International’s guidelines on epoxy adhesives
It was necessary to test each factor behind the epoxy resin not curing problem. The applicator claimed the mix ratio was correct, but I still reviewed the batch records and checked weighing accuracy. The site temperature was 16°C, which was not ideal. Humidity was above 75%, and either condition could slow curing. I also inspected the raw material storage. The hardener drum had absorbed moisture because it was left partly open. This revelation explained why the epoxy remained sticky.
3. The chosen solution and how to use it
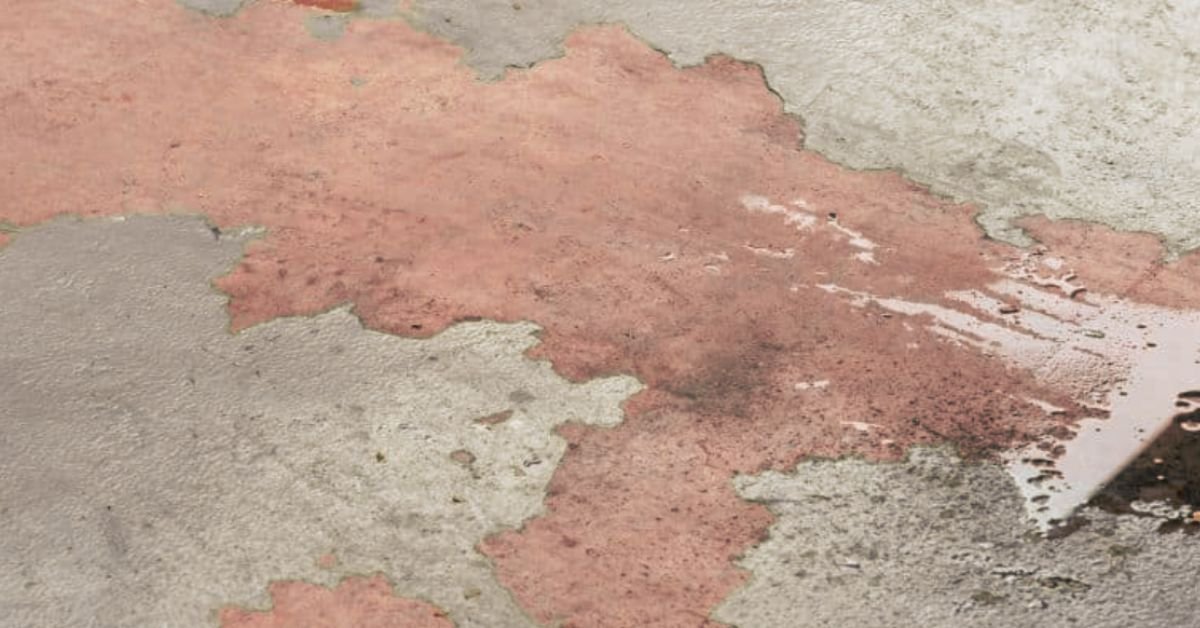
Image Credit: Epoxy Colorado – How to Repair Damaged Epoxy Flooring
You can see in the picture below that you need to carefully remove the uncured epoxy layers before putting them back on. If you skip this step, flaws will be trapped under the fresh coat. Cleaning with solvents and removing mechanically brings the surface back to good condition for the following coating. This was the most important part of my case study since it made sure the remedy lasted.
I picked a controlled technique to resolve the epoxy resin not curing issue. Options included changing the resin, applying heat, or adding new hardener. Adding extra hardener was risky since it could cause brittleness or poor bonding. Heating alone couldn’t correct the chemistry that had already been contaminated by moisture.
- The greatest thing to do was
- Use scrapers to get rid of the uncured epoxy coating.
- To get rid of any leftover material, clean the surface well with solvent.
- Use new, dry resin and hardener to put on a new layer of primer.
- Make sure the mixing ratio is right: 100 parts resin to 50 parts hardener by weight.
- To make sure the mixture is even, use a slow-speed drill to mix it for at least three minutes.
- Use blowers to raise the temperature at the location to over 20°C.
- Use dehumidifiers to keep the humidity level below 65%.
This step-by-step method ensured the epoxy resin not curing problem did not return. To improve curing stability, I modified the formulation by adding a small amount of accelerator. This adjustment allowed the resin to crosslink faster, especially in cooler climates.
4. Results and Improvements After Fixing Epoxy Resin Not Curing
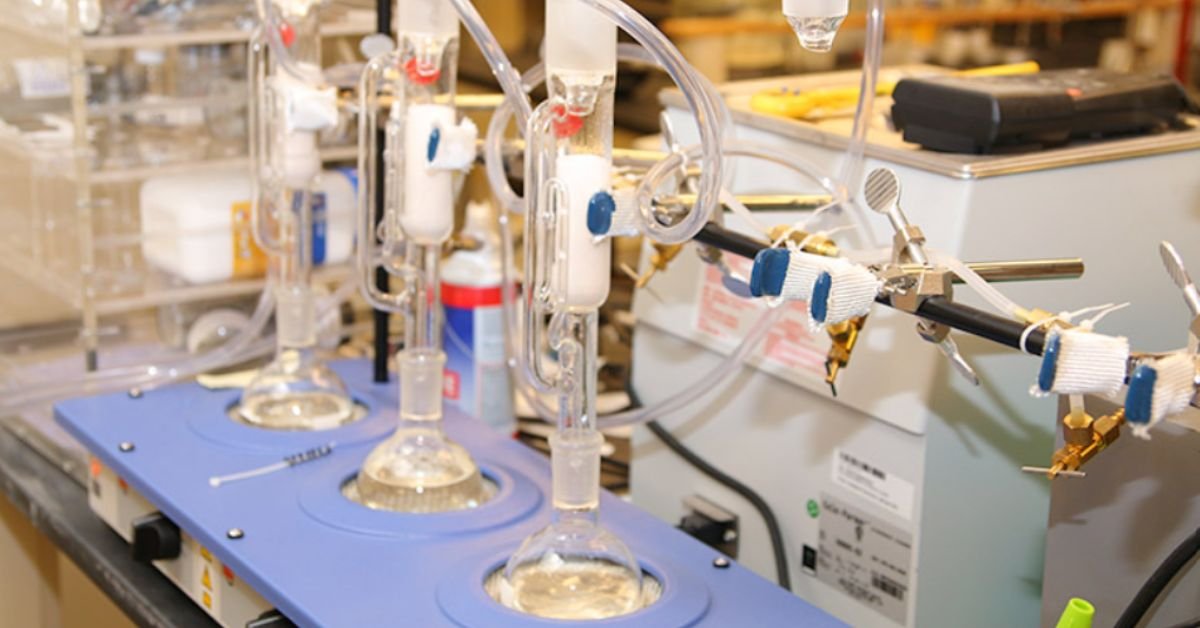
Image Credit: Team AET – Chemistry Laboratory Services
There is always lab verification behind every field solution. The picture below displays a chemical lab where epoxy resin and hardener are tested for their curing capabilities. These kinds of controlled tests help us find problems like moisture contamination or improper ratios, so we can be sure that the changes we make on-site are dependable.
The outcomes of fixing the epoxy resin not curing issue were clear. The new layer dried within 16 hours. After 24 hours, the surface was firm and load-bearing. Pull-off adhesion increased from almost zero to 3.2 MPa, well above the client’s requirement.
Before it was fixed, the floor was dirty, sticky, and not useable. The surface had a homogeneous shine and was very resistant to chemicals when it was fixed. The client was happy, and the people who applied the product felt more confident in using it.
A new perk came up. Setting up a controlled atmosphere with dehumidifiers also made it more comfortable to work and cut down on the need to redo work in nearby regions. Adding the accelerator became a common change for projects in cool, humid areas in my product line.
5. Tips to Avoid Epoxy Resin Not Curing Issues
Don’t worry if your epoxy isn’t setting. First, check the mix ratio, mixing time, and site conditions. Use items that are always new and dry. Adding more hardeners as a shortcut is never a good idea because it typically makes things worse. Whenever you can, keep the curing temperatures over 20°C. Buy dehumidifiers if you live in a humid area.
Furthermore, keep track of the weather and the mix for each batch. Keeping accurate records might save you a lot of money in the long run. Don’t merely hide a failure if it happens. Identify the underlying cause, remove the problematic layers, and reapply them correctly. If you treat epoxy chemistry with care and respect, it will forgive you.
Conclusion: Final Thoughts and Relevance to the Industry
It might be annoying to resolve problems using epoxy, but it is possible. In my case, the issue stemmed from the wetness of the hardener and the poor condition of the location. By fixing materials, managing mixing, and stabilizing the atmosphere, we restored performance.
The main point is that epoxy is a strong chemical that needs to be handled with care. You won’t have many difficulties with curing if you follow the ratios, conditions, and storage regulations. And if you do, keep in mind that the solution is to carefully figure out what’s wrong and then reapply it in an organized way.
This experience not only rescued a big project, but it also taught me how to avoid making the same mistakes again. If you deal with construction chemicals, the most important thing to remember is to never give up on cultivating discipline.
Disclaimer: Images used in this blog are sourced from external websites for educational and illustrative purposes only. Full image credits have been provided to the respective owners.
Last updated on August 29, 2025
As Buildchemx’s founder, I’m Amarender Akupathni, who has over ten years of experience in the R&D of construction chemicals. I have a background in biotechnology, marketing, and chemistry, and my areas of expertise are adhesives, coatings, and environmentally friendly solutions. I offer useful perspectives at Buildchemx that connect laboratory studies with on-site implementations.